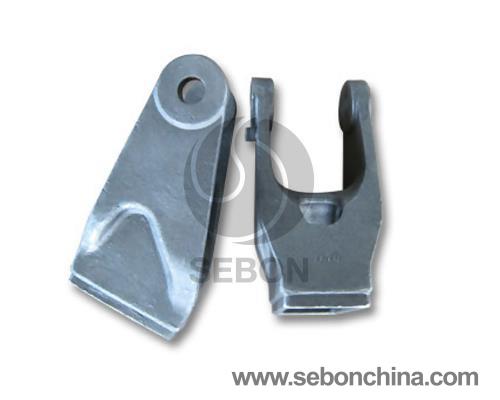
Stainless steel precision casting process
1, Precision casting mold First, based on the products of different shapes. The mold parting on the lower die, by car, plane, milling, erosion, EDM process is completed. Half of a pit shape, size, with the product is consistent. Because the wax mold is mainly used for industrial wax-pressure use, so the choice of a high melting point, high hardness, lower requirements, cheaper, lighter-weight aluminum alloy material mold.
2, the use of aluminum mold to produce a large number of industrial the wax solid core model. Under normal circumstances, an industrial the wax solid core model corresponds to only out of a rough product.
The industrial waxes real surrounding margin of wax mold finishing, deburring after more than a single wax mold stick (also known as group tree) and pre-prepared mold head, this die is a wax model production core model. (Looks much like a tree)
4, will have been fixed in the die head multiple wax mold is coated with industrial glue evenly spray the first layer of fine sand (a refractory sand, high temperature, usually with silica sand). This small particles of sand, very fine, this will ensure that the final rough surface is as smooth as possible.
5, let set at room temperature (or thermostat) spray wax mold of the first layer of fine sand to dry naturally, but it can not affect the internal the wax mold shape change, natural drying time depends on the product itself, the internal complexity of general fine casting first time to air dry in about 5-8 hours.
6 first sand spraying and dry naturally after the in wax mold surface to continue on industrial glue (silicon soluble), and spray the first two-story sand before the second layer of sand particle size than the first layer of sand come to coarse. Finished spraying the second layer of sand set thermostat wax mold to dry naturally.
7, after the second sand spraying and dry naturally, and so on for the third sandblasting, the fourth sandblasting fifth sandblasting process. Requirements:
- Required under the surface of the product, the volume size, dead weight and the number of corresponding adjustment sandblasting. Under normal circumstances the blasting times is 3-7 times.
- Each sandblasting grit size are not the same, usually after the procedure grit than those of the coarse sand of the former procedure, dried are not the same length of time. Generally a wax mold sand production cycle for about 3 to 4 days.
8, will have to complete a wax model of the blasting process before the baking step, and then evenly coated with a layer of white industrial latex (Silicon soluble) to play a bonding and curing sand, and sealing wax mold for the post Road baking process to prepare. The same time in the baking process, but also improve the brittleness of the sand, easy crack sands, remove the rough.
9, the baking process
Fixed into the metal sealed in the wax mold die head and blast air-dried process the special oven heating (commonly burning kerosene vapor furnace). Due to industrial December melting point is not high, the temperature is about 150 ゜, wax mold heat melted a wax water outflow along the gate, this process is a lost-wax. Finished off wax wax mold is just an empty shell sand. Precision casting the key is to use this with an empty shell of sand. (Usually wax can be used repeatedly many times, but these wax must be re-filtered, otherwise not clean the wax will affect the quality of rough surface, for example: the surface of the sand holes, pits, and at the same time will also affect the shrinkage of the casting products).
10, baked sand shell
Sand shell finished off the wax more sturdy and solid, poured into a stainless steel water before baking sand shell, usually at high temperature (temperature about 1000 ゜) stove baking.
11, the already high temperature dissolved into the liquid stainless steel water poured into finished off the wax shell sand, until liquid stainless steel water is full of wax molding space, until completely filled, including the part of the middle of the die.
12, because the materials have different ingredients mixed melting stainless steel boiler, the factory must detect material percentage. Release and then be adjusted according to the desired ratio, such as the increase in those aspects of the elements, to achieve the desired effect.
13, liquid stainless steel water cooled and solidified, by means of a machine tool or human after the outermost layer of the sand shell crack, exposing the solid stainless steel products is the original wax mold shape, that is, the final desired green sheet. Then individually cut separation kibble on a single rough pieces.
14, the test blank: Surface trachoma, stomatal blank must repair welding with argon, when the waste cleaning and re-melted.
15, cleaning rough: rough must have passed the test after the cleaning process.
16, other machining processes, until the finished product.